Flatbed AGV
A Flatbed AGV (Automated Guided Vehicle) is a type of robotic vehicle used in industrial and warehouse settings for material handling and logistics tasks. As the name suggests, a flatbed AGV is designed with a flat, open platform or deck on which materials, products, or equipment can be placed and transported. These AGVs are used to move loads from one location to another autonomously, without the need for human intervention.
Key features and characteristics of Flatbed AGVs include:
1. Flat Platform: The defining characteristic of a flatbed AGV is its flat and open platform or deck. This platform is designed to accommodate various types of loads, such as pallets, containers, bins, or custom fixtures, depending on the specific application.
2. Payload Capacity: Flatbed AGVs are designed to carry a wide range of loads, including heavy and bulky items. The payload capacity can vary depending on the size and configuration of the AGV.
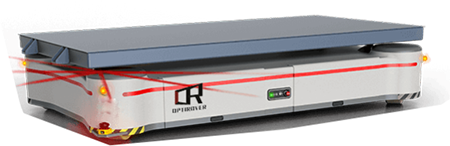
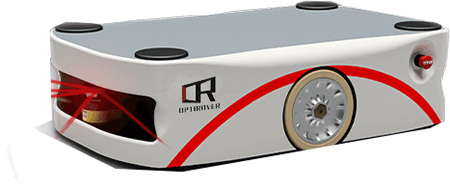
1. Navigation: These AGVs are guided by various navigation systems, including laser-based systems, magnetic tape, or vision-based technologies. They use these systems to follow predefined paths or navigate autonomously in dynamic environments.
2. Safety Features: Flatbed AGVs are equipped with safety sensors, cameras, and collision avoidance systems to detect and avoid obstacles, ensuring safe operation in shared spaces with humans and other machinery.
3. Versatility: Flatbed AGVs are highly versatile and can be used in a variety of applications, including material transport, assembly line support, and warehouse logistics.
4. Integration: They can be integrated with other automation systems, such as conveyor systems, robotic arms, and warehouse management software, to create an efficient and seamless material handling process.
7. Efficiency: By automating material handling tasks, flatbed AGVs can improve operational efficiency, reduce labor costs, and minimize the risk of workplace injuries.
8. Customization: Some flatbed AGVs are designed to be highly customizable, allowing users to adapt the platform and attachments to specific load requirements and applications.
Flatbed AGVs are commonly used in industries such as manufacturing, automotive, aerospace, logistics, and distribution. They play a crucial role in streamlining material transport processes, reducing manual labor, and increasing the overall efficiency of warehouse and production operations. The ability to transport a wide range of loads on a flat platform makes them valuable tools for businesses looking to automate their material handling tasks.
A Counterbalance AGV (Automated Guided Vehicle) is a type of robotic vehicle used in industrial and warehouse settings for material handling and logistics tasks. It is designed to carry and transport goods within a facility autonomously, without the need for human intervention.
The term “counterbalance” in Counterbalance AGV refers to the vehicle’s design and functionality. These AGVs are equipped with a counterweight, often located at the rear of the vehicle, to balance the weight of the load they are carrying. This counterbalance ensures stability and helps prevent the AGV from tipping over when lifting and moving heavy loads.
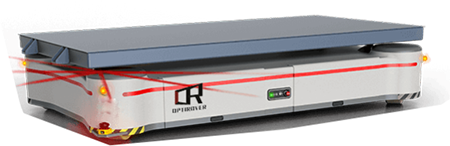
Key features and characteristics of Counterbalance AGVs include:
1. **Counterweight:** The counterbalance at the rear of the AGV offsets the weight of the load being carried, ensuring that the vehicle remains stable during operation.
2. **Lifting Mechanism:** Many Counterbalance AGVs are equipped with a lifting mechanism, such as forks or a platform, to pick up and transport pallets, containers, or other materials.
3. **Navigation:** These AGVs are guided by various navigation systems, including laser-based systems, magnetic tape, or vision-based technologies. They use these systems to follow predefined paths or navigate autonomously in dynamic environments.
4. **Safety Features:** Counterbalance AGVs are equipped with safety sensors, cameras, and collision avoidance systems to detect and avoid obstacles, ensuring safe operation in shared spaces with humans and other machinery.
5. **Payload Capacity:** Counterbalance AGVs are designed to handle relatively heavy loads, making them suitable for tasks that involve transporting bulky or substantial materials.
6. **Applications:** They are commonly used in manufacturing plants, warehouses, distribution centers, and other industrial settings to automate tasks like moving raw materials, transporting finished products, and replenishing inventory.
7. **Efficiency:** By automating material handling tasks, Counterbalance AGVs can improve operational efficiency, reduce labor costs, and minimize the risk of workplace injuries.
8. **Flexibility:** These AGVs can be programmed to perform various tasks, and their routes can be adjusted or reprogrammed as needed to adapt to changing production or logistics requirements.
Counterbalance AGVs are just one type of AGV used in industry, and their design and capabilities may vary depending on the specific needs of the application and the manufacturer. They play a crucial role in modern industrial automation and logistics, helping businesses streamline their operations and improve overall efficiency.
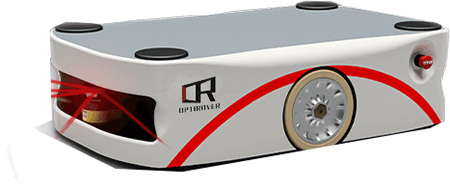