AGV Path Planning
Natural navigation AGV refers to a mobile robot that realizes self-navigation based on SLAM (simultaneous localization and mapping) technology without the need for any external identification such as magnetic strips or QR codes. In recent years, in order to highlight the product’s Characteristics, the industry began to use the term AMR (Autonomous Mobile Robot), hoping to differentiate it from traditional products.
AMR “broadly” refers to mobile robots with strong autonomy.
Generally, it needs to have rich environment perception capabilities, on-site dynamic path planning capabilities, flexible obstacle avoidance capabilities, global positioning capabilities, etc. It can actively react to the light in the environment and avoid obstacles moving in the environment.
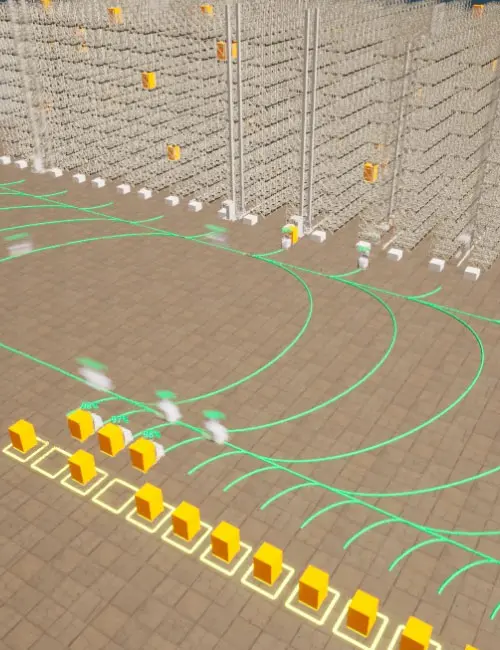
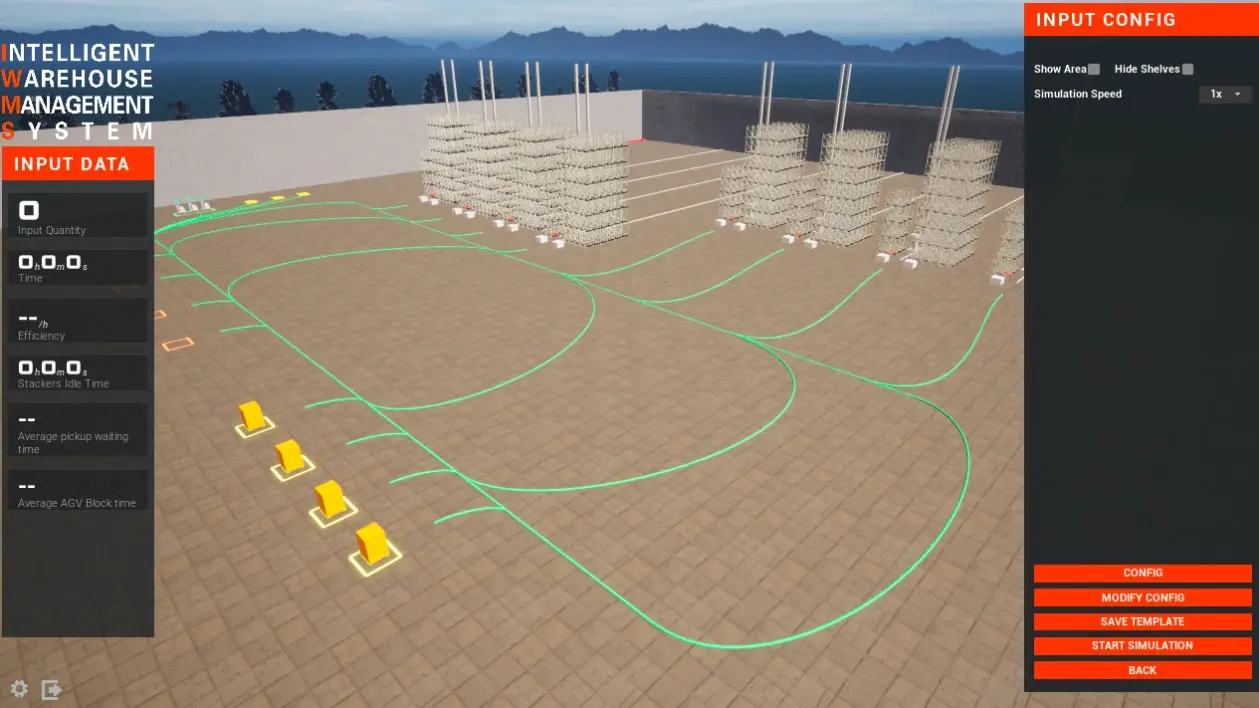
System Introduction
With the further development of market cultivation, the recognition of natural navigation AGV/AMR on the application side is gradually increasing, which will be conducive to the rapid expansion of the subsequent market scale.
At the same time, with the development of manufacturing, the demand for manufacturing flexibility increases, product cycles are shortened and accelerated, labor costs rise, and the demand for human safety in the use environment increases, all of which require manufacturing and logistics scenarios to have rapid response capabilities and higher efficiency.
Natural navigation AGV/AMR, highly automated flexible handling equipment, will be the future.
System Advantages
In this supply chain, the AGV autonomous positioning and guidance system has become particularly important, which determines the AGV’s own positioning, path planning and decision-making. We have designed an algorithm platform that contains a variety of algorithms, which can freely combine various visual algorithms and route algorithms to quickly plan and form a scientific and easy-to-deploy AGV robot working route, assisting the system to achieve optimal efficiency and safety. method to complete the tasks in the production scenario.